Welcome to the Rare Woods South Africa Woodworker Sessions interview series. Here, we hope to discover more about what makes our woodworkers tick, how you became involved in the craft, how and why you build your pieces and maybe learn a few secret techniques and tips along the way!
Our interviewer, a woodworker since the age of 8, Tobias Lochner is no stranger to the workshop. Find out more about him here.
In issue #002 of The Woodworker Sessions South Africa, I chat to passionate Cape Town based mid-century-modern furniture maker, David Harker. We hope you enjoy the interview and please feel free to leave a comment.
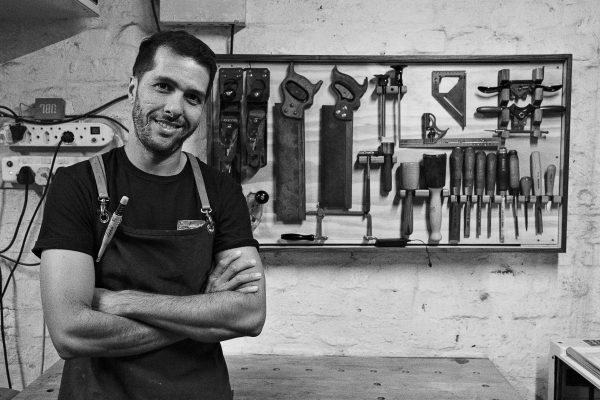
Question #1
Tobias: Hi Dave. Thank you so much for joining The Woodworker Sessions. Please would you tell us a bit about yourself, what is/was your career, a little about your family and how you became a woodworker.
Dave: I am an electronics engineer by day in the field of industrial automation. I am married and dad to my gorgeous little girl!
I grew up in a woodworking family. My father was a professional woodworker and owned his own business. It is very sad that I only began woodworking as a hobby after my dad had passed on. Although I spent many hours (mainly on weekends) working as an assistant in his workshop, I had no interest whatsoever at the time in the craft. It was only some years after his passing that I picked up the craft and have never looked back. Unfortunately, by then all of my dad’s tools and machinery had been sold off. There are definitely still occasions when I wish that he was still around so I could ask for advice or just have a shoulder to lean on.
Question #2
Tobias: How did you get started in woodworking and how long have you been a woodworker?
Dave: I started woodworking in 2014, inspired by my father in law who is based in Germany. He visited us in South Africa and wanted to assist me with a few DIY projects around our house. I was completely blown a way at how he went about tackling and planning projects. He is a mechanical engineer by profession, and an extremely handy woodworker! By the time he returned to Germany, the woodworking bug had bitten me hard!
I then tackled a few small builds around our home and after some research, I decided to build my own hollow wooden surfboard. I was intrigued with the idea that I could surf with a board that I had made myself from natural materials.
After the success of this project, my woodworking journey began in earnest.
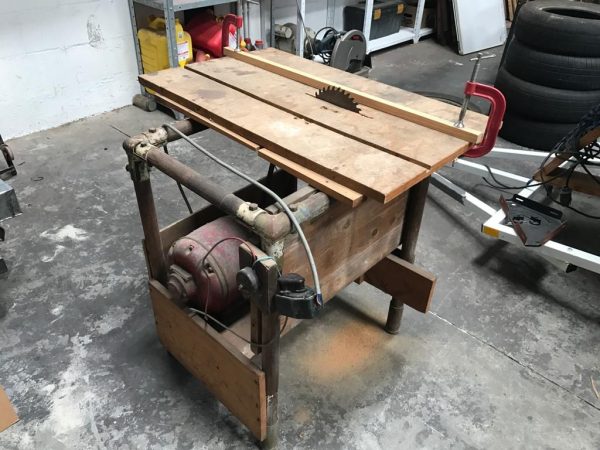
Question #3
Tobias: What was the first item that you made and which is your favourite piece?
Dave: The first furniture piece I made, was a small media unit. It was constructed from laminated pine and I used screws and glue for the joinery. It was a very simple project, but badly needed for an awkward space in our living room.
My favourite that I have made thus far is definitely my Danish inspired loung chair in memory of my father. I call it the “Gordon James Chair”.
It is made from American Black Walnut and the secondary wood used for the seat and backrest slats is Beech. I spent months designing this chair, factoring in strength, aesthetics and ergonomics. A chair is a dautnting build and with the aforementioned factors can be a real give-or-take between the three. The actual build was not an entirely difficult process, I found the design much more challenging.
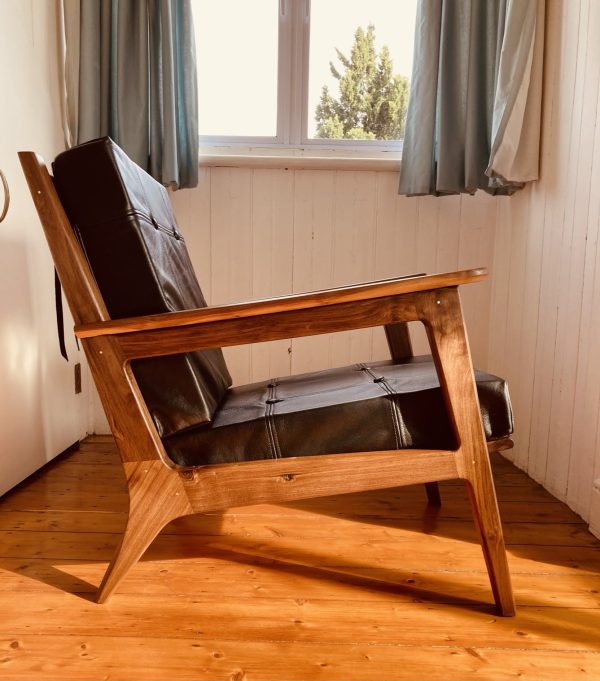
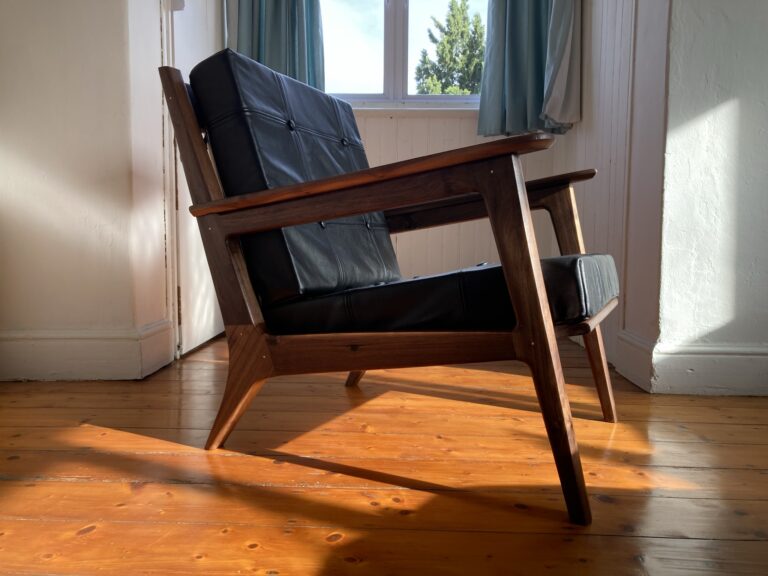
Question #4
Tobias: Which style of furniture do you enjoy building the most?
Dave: It’s no secret that I have a love affair with Mid-Century and Danish furniture. In recent years I have steered towards the latter.
Mid-Century furniture is known mainly for utilitarian pieces and has very little focus on joinery and curved elements. Danish furniture is much more well thought out, with curves and details designed by some of the very best furniture designers of the 20th century. I also enjoy the mix and interplay between the two styles as there is a very close link between the two.
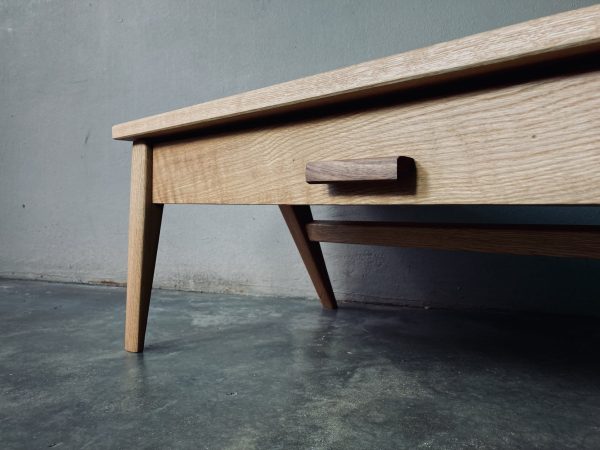
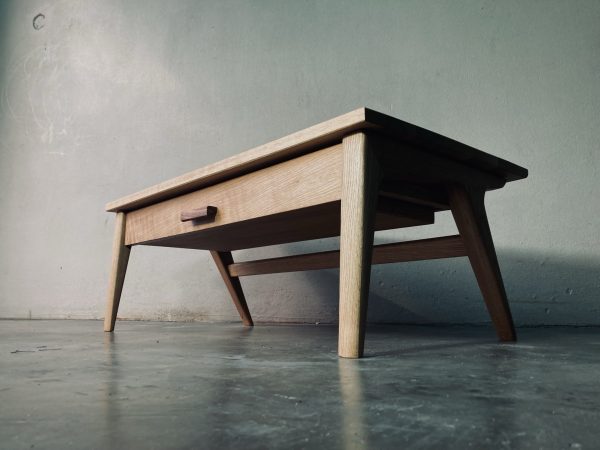
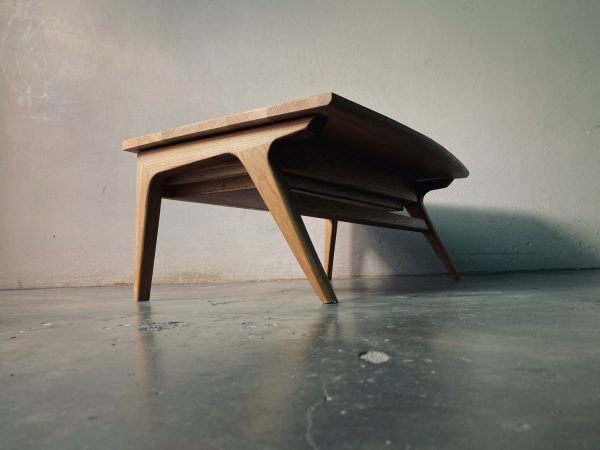
Question #5
Tobias: Which are your favourite local lumber species and which are your favourite exotics to work with?
Dave: When it comes to wood species, I try and stick with the more subtle and less contrasting woods. My favourite African lumber is definitely African Mahogany. Black Walnut and White Oak are my two favoured exotics species, as they offer two great options to my clients – light or dark. All three of these species are a pleasure to work with using hand tools, power tools and machines, while giving the classy look that I strive for in my pieces.
I tend to opt for contrasting species for small details and accents only. I believe that using these species sparingly allows the beauty of the wood itself to be accentuated and therefore more appreciated.
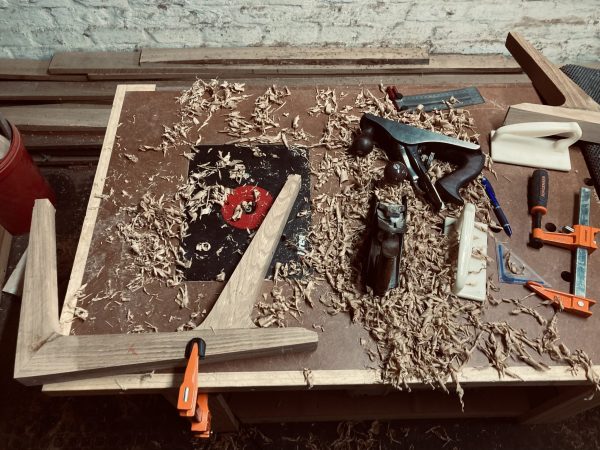

Question #6
Tobias: Please list your most used hand tools and tell us why they are your “go-to” tools.
Dave: My favourite hand tools seem to change all the time. I love using block planes mainly when working on fine details when finishing. It’s always exciting when a furniture piece starts taking shape and using block planes and card scrapers allows my to fine tune my project, rather similarly to fine tuning a musical instrument. The extra touches make all the difference.
Recently I started to enjoy my spokeshaves. My concave spokeshave has definitely become a new favourite hand tool. I use it primarily for shaping the legs on my pieces. Also, as basic as it may be, my #4 hand plane is always at hand for shaping and finishing. I use it on every project and it is the one hand tool that I could not do without!

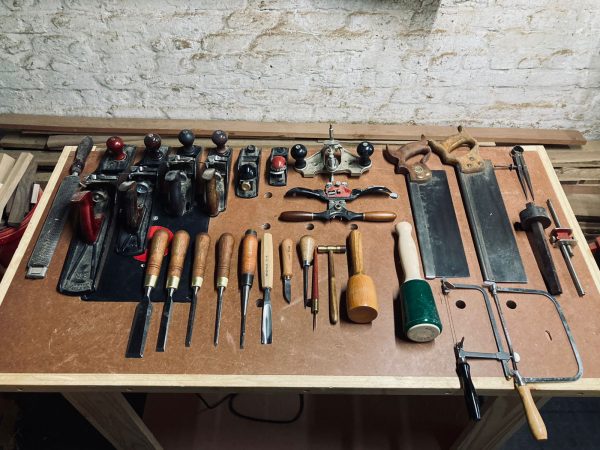
Question #7
Tobias: Can you list your favourite power tools and machines and tell us why?
Dave: Routers are definitely my absolute favourite power tools. I have a number of them specifically set up for various dedicated tasks. The possibilities with these tools are endless.
The bandsaw is by far my favourite stationary machine. It allows one to be extremely creative… cutting straights or curves. In my opinion, It is a machine that encourages one to be artistic.
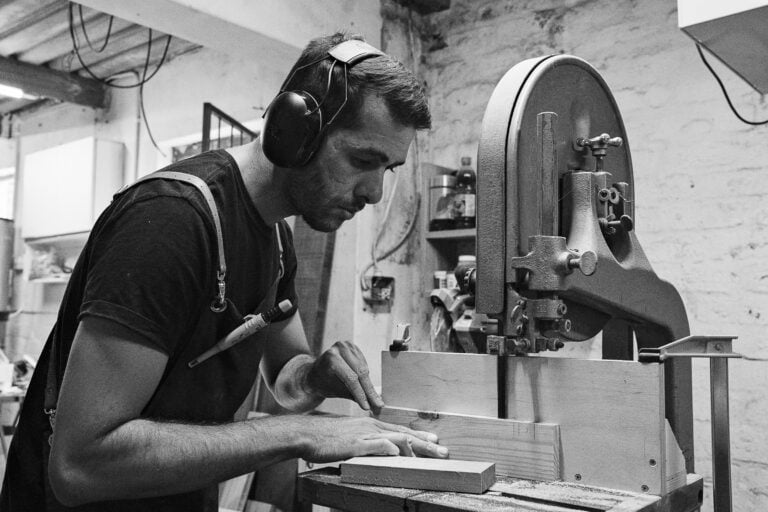
Question #8
Tobias: What is it about woodworking that you find the most enjoyable?
Dave: When working with my hands and more specifically with wood, it seems like the fast-paced world we live in “pauses”! I become extremely focussed on shaping and working a pile of rough boards and I find I am not overthinking things, but am simply enjoying the process.
Woodworking allows me to explore my creativity, which is something that is extremely difficult in the field of engineering.
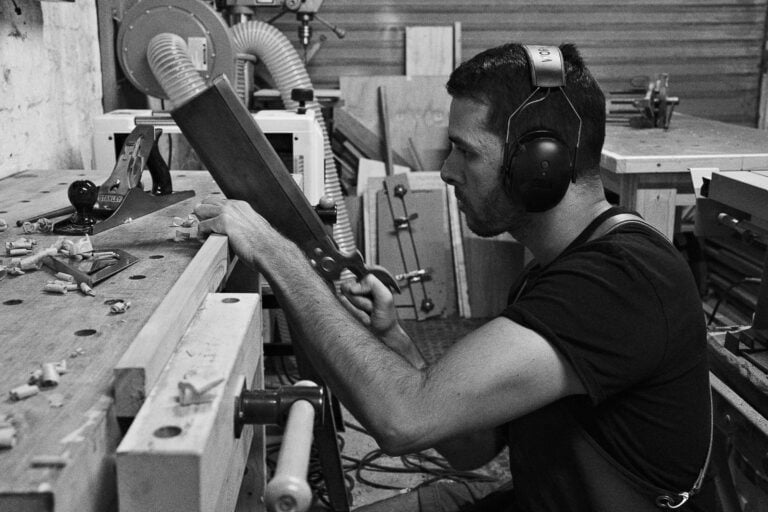
Question #9
Tobias: What type of workshop do you have and how has it evolved over time?
Dave: I work in the same garage where my dad started his woodworking business. It is a tandem garage.
As we all know, one never has enough space! There is something really special about being in this space as my dad began his career almost 40 years ago in this very garage! I hope to expand the workshop soon as I am really outgrowing my current floor space.
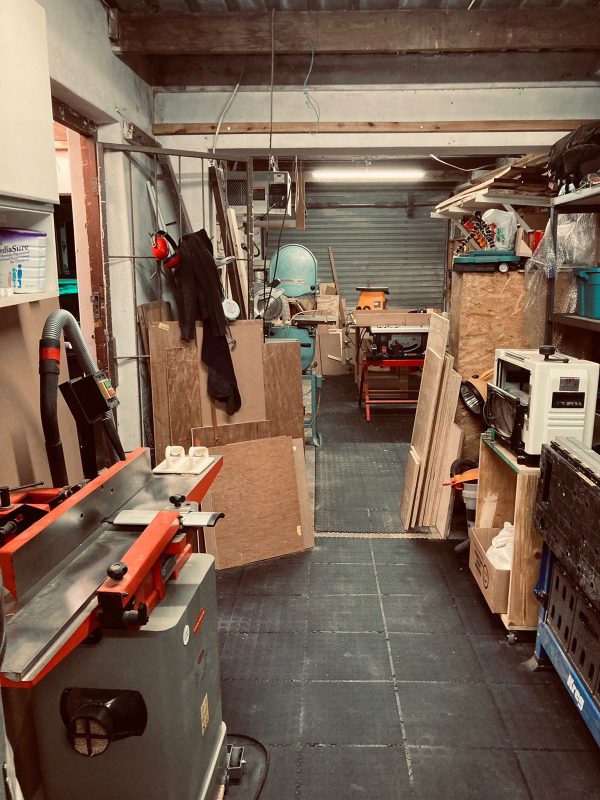
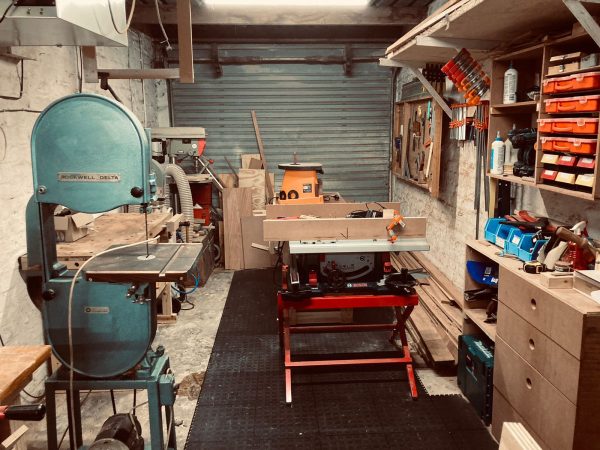
Question #10
Tobias: What is your clamp line-up and why?
Dave: My clamp line-up consists mainly of Jorgensen “F” style clamps and they are limited in length. For bigger assemblies, I use old heavy “T” bar clamps. I am hoping to upgrade to a good number of pipe clamps soon. Apparently you can never have enough clamps, in my case I have way to little!
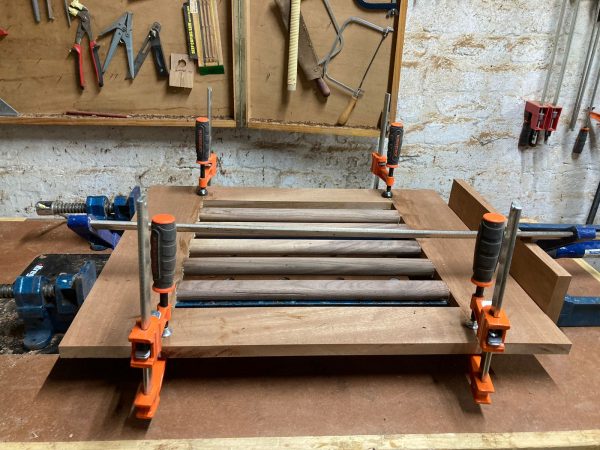
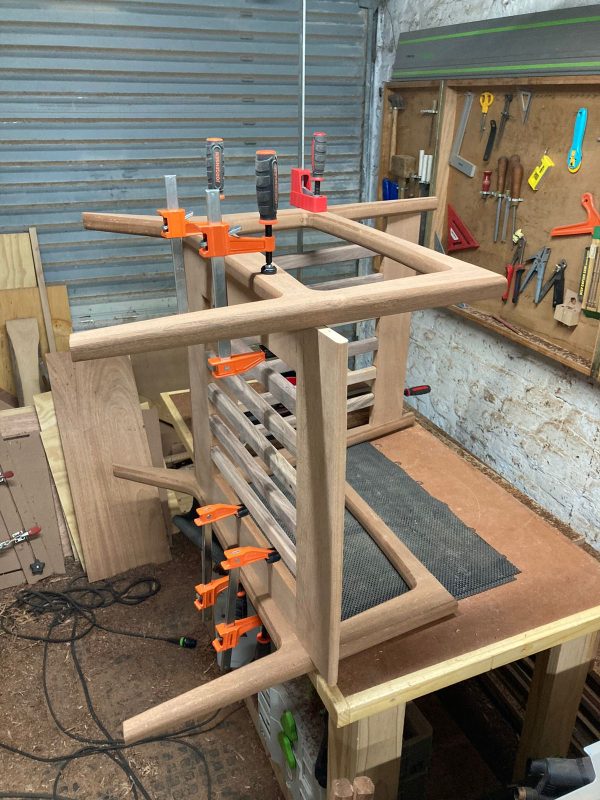
Question #11
Tobias: Which adhesives do you use and why?
Dave: I use Alcolin Professional for glueing up lighter coloured woods and Alcolin Ultra for darker species. I find that Alcolin Ultra tends to leave dark seams on joints and this is more noticeable on lighter woods.
My adhesive choice also boils down to the specific requirements of an application and not just the colour in my builds.
Question #12
Tobias: Which woods (exotic and local) have you not yet used and why are you interested in building with these species?
Dave: There are a few that I am itching to try and they are predominantly African species. I recently purchased some exquisite Sapele from Rare Woods SA and am extremely excited about using it. Sapele was extensively used in the original Mid-Century pieces that I am hoping to re-create very soon.
African Rosewood is also a species that has caught my attention and the ruby, reddish- brown is very appealing!
Lastly, Zebrano is another beautiful species that I have on my list. I would however use it sparingly for specific accents and details as previously mentioned.
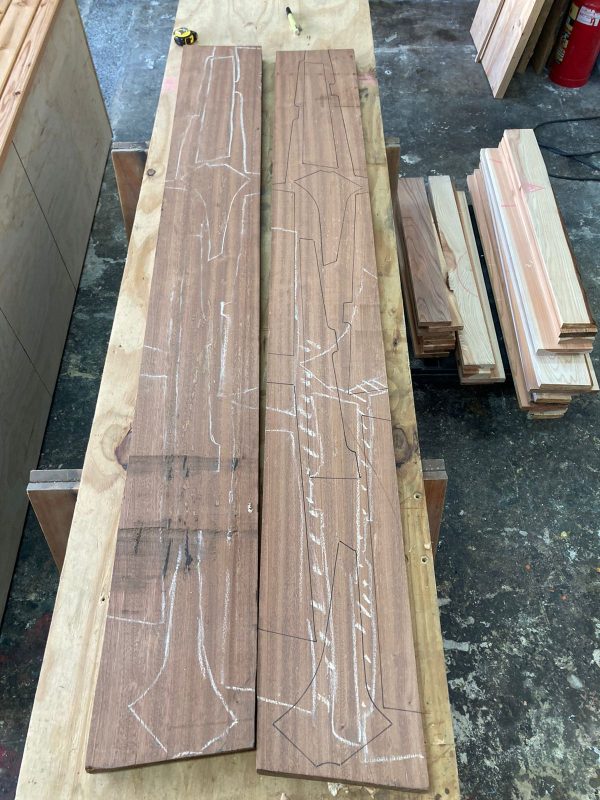
Question #13
Tobias: What and whom are your sources of inspiration for your craft?
Dave: I tend to draw inspiration not only from other woodworkers, but other makers in general. I enjoy reading about original pieces from yesteryear and about why and how these pieces were made. I am a firm believer that we can learn an immense amount from past furniture makers.
If I had to narrow it down to a few current woodworkers that inspire me, Philip Morley would top my list! Jory Brigham is another great builder that I follow closely. As a craftsman, ~Craig Thibodeau is simply on another level completely and I found his book “The Craft of Veneering” essential in a number of my builds.
Lastly, from a local woodworking perspective, it has to be you, Tobias!
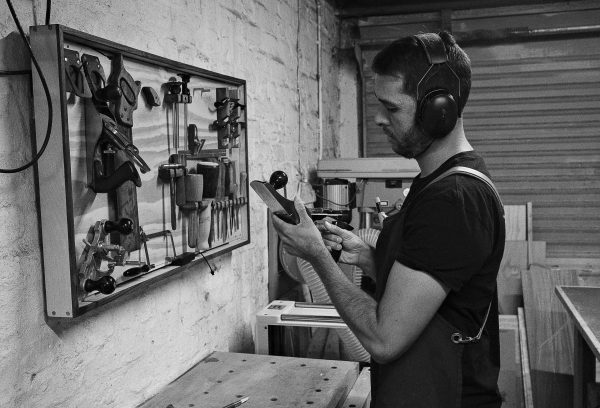
Question #14
Tobias: How do you design your pieces? Do you use CAD or SketchUp? Do you sketch out by hand?
Dave: In the past, I generally sketched out my pieces by hand and only in recent years have I started using SketchUp.
My current process is to design a piece in my head for weeks on end before I put pen to paper and only once the design starts to properly take shape on paper, do I finally move on to SketchUp.
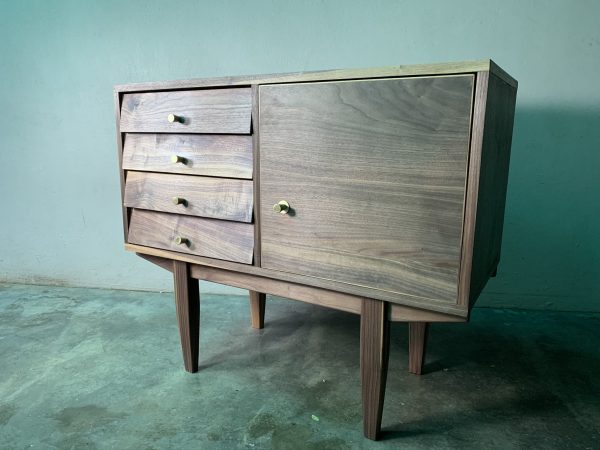
Question #15
Tobias: What are your finishing regimes, which products do you use and which are your favourite processes?
Dave: I have played with my fair share of finishes. I do however, prefer hard wax finishes. Hard wax finishes give a natural feel and look to the wood.They are also durable and allow one to rework a piece without much hassle. My preferred hard wax oil finish is Osmo Polyx 3032 Satin.
I am yet to experiment with shellac. I am very intrigued by shellac, as this was used on furniture dating from the late 1700’s right up to the 1950’s.
Making my own finishing wax is a project that I will tackle very soon.
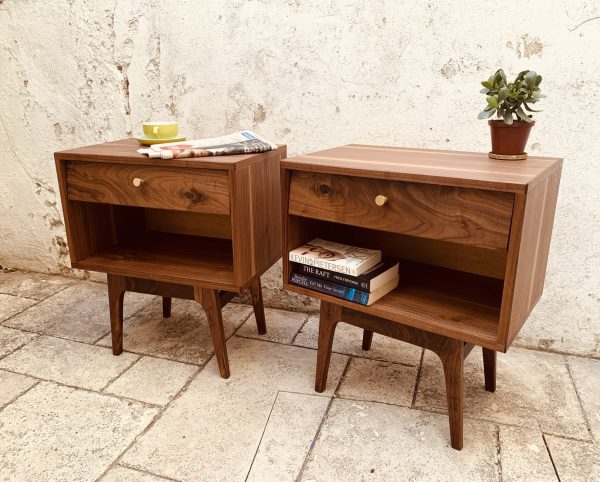
Question #16
Tobias: Which parts of working with wood do you dislike the most?
Dave: Dust is the most disliked aspect of woodworking for me, as is the case with most woodworkers. Dealing with wood dust from a health point of view and keeping my workshop clean is my biggest gripe in the craft.
Question #17
Tobias: Which music do you enjoy listening to whilst working in your shop?
Dave: I listen mainly to acid jazz, indie and alternative folk, rock and metal. It’s quite an eclectic mix. I steer clear of podcasts as I find them distracting, especially when I am working with machinery.
Question #18
Tobias: What is your tool sharpening regime?
Dave: I use Japanese ceramic whetstones, starting at 1000, through 3000 and finishing off at 6000 grit. After working through these three stones (depending on the level of sharpening required), I use a leather strop loaded with buffing compound to finish the arris.
I also have a Tormek whetstone grinder, although I use it mainly to sharpen knives and odd hand tools with different profiles.
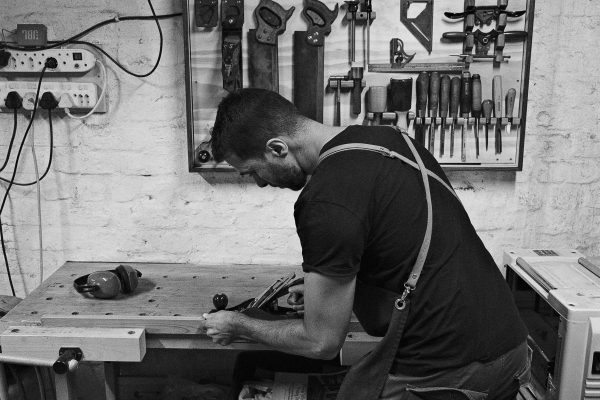
Question #19
Tobias: What custom jigs or tools have you specifically developed for your woodworking?
Dave: I use custom jigs on all of my furniture builds. The primary jigs are various table saw sleds for specific furniture parts and I have developed them to tie in extremely well with my workflow, when I’m working off any of my multitude of templates. I take care in making templates and jigs, so that they can be used repetitively for future builds.
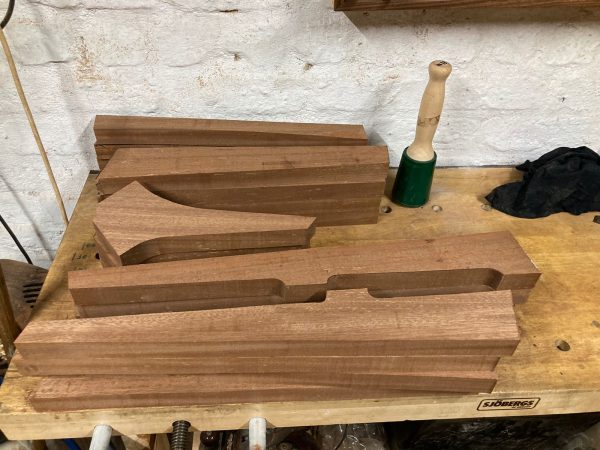
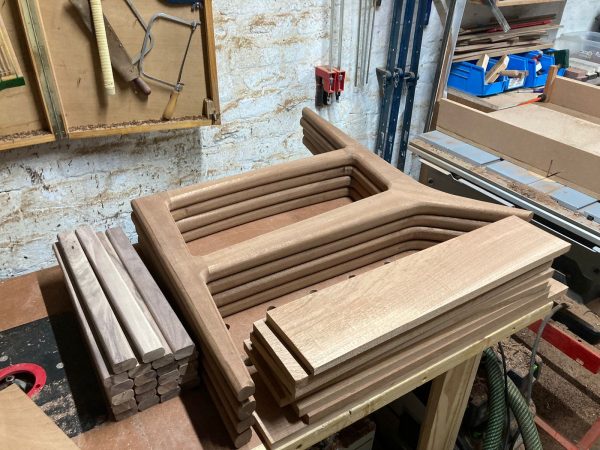
Question #20
Tobias: What is the next piece you are going to build and why?
Dave: Currently, I am planning two lounge chair builds. They will be somewhat similar to the “Gordon James” chair, but with small differences. They will be both be made from a single stunning 76mm thick Sapele beam that I was extremely lucky to pick up at the recent Rare Woods SA Febfest sale! (Can’t wait for Febfest 2023).
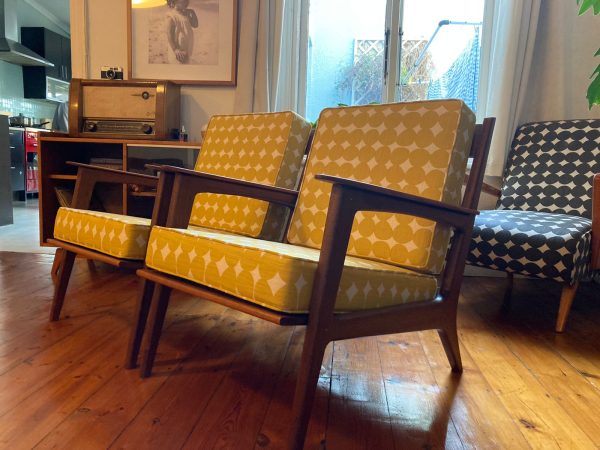
Tool Wishlist
- 3HP Cabinet style Table Saw
- 18″ 3HP Band Saw
- Veritas Tools Low Angle Jack Plane with 3 different blades
- Veritas Tools Convex Spokeshave
- Veritas Tools Scrub Plane
- Sets of Parallel Jaw Clamps in various lengths
Lumber Wishlist
- American Black Walnut
- Zebrano
- Various Rosewoods
Makers with whom I would love to spend time
- Philip Morley
- Jory Brigham
Links
- Instagram: @davehark101
- Instagram: @midmodernfurniture
- Email: davehark@gmail.com